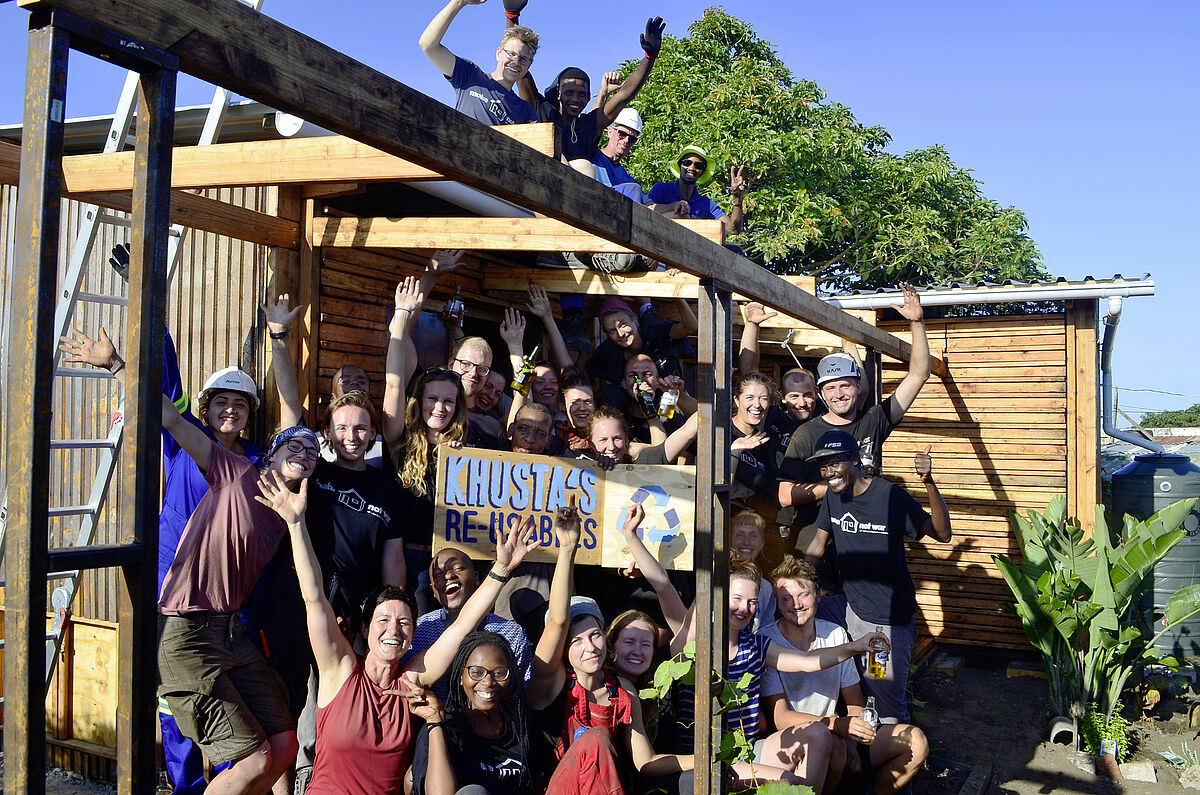
A Workshop for Khusta
Walmer Township, being the oldest township in Port Elizabeth (PE), is one of the very few townships in South Africa that were not relocated during the Apartheid era. Therefore it still contains a typical "organically grown" housing structure, ranging from one-room-shelters and informal shacks to recently built RDP*-houses.
Especially in the informal part of the settlement where the projected building is going to be implemented, people's living conditions are extremely difficult due to unemployment, poverty and the lack of sanitary facilities.
Waste is a big issue, not only in the Townships but within the whole country. Piles of rubbish pollute almost every public space and strips along roads. Informal waste picking has developed into a common “business model” of members of the poor population, collecting reusable and recyclable goods from the streets and selling them.
One oh those waste pickers is Khululekile Moko, alias Khusta. He has been living in Walmer Township for almost his entire life. After losing his job in a manufacturing company, he started to make a living out of collecting trash. He is also technically gifted and capable to repair almost anything, making him a point of contact for the whole community.
In order to improve his working conditions we decided within the project team to build a workshop with additional rooms for secure storage of the recycling material. We will also replace the existing old bucket toilet and integrate it within the new structure.
* Reconstruction and Development Programme – A governmental housing programme, aiming at adequate housing for every South African citizen.
PHASES OF IMPLEMENTATION
1. Background
The first step towards the "Joint Action Project 2020" is conducted by the four German and the six South African students participating in a newly established exchange programme. Supported by research and ideas contributed by a team of fellow students in Germany, they jointly develop the project concept, identify a suitable construction method, based on the assessment of the local situation in the township and on Khusta's property. Most importantly they get to know Khusta, his wife, and his neighbours, talk to them, and learn about their living situation and needs.
2. Design
The overall layout is developed during various workshops at Nelson Mandela University. The project´s participatory approach and background knowledge about about the meaning and significance of development, human settlements in South Africa, and the history of Walmer Township feed into the design. The final concept is a collaborative result of hours of research, discussion, and design work in Germany and South Africa. The workshop is going to be an L-shaped building framing an open veranda (in South Africa commonly known as “stoep”), facing the private section of the property, providing space for repairs and other handicraft activities.
3. Site Preparation
As Khusta's property is crammed with plants, collected recyclables, and other things our first mission is to clear out the space required for the new structure. During this part of the implementation, we are in constant exchange with Khusta: What needs to be preserved? Which things are we allowed to throw away? Where should all the plants go?
4. The Assembly
Our recycled building material originates almost entirely from outsourced packaging for truck parts from a local automobile manufacturer. Khusta's property is small and has just one narrow entrance (1.10 m width). For this reason, the building needed to be prefabricated in modules and put together on the property. The preparation and prefabrication will be mainly carried out in our work area („Makerspace") in PE Central. Being supported by Port Elizabeth TVET College, we are also going to use workshop facilities of the college´s Iqhayiya Campus.
4.1 Foundation
Containing a high percentage of backfilled soil, sandy and organic material, the sloping ground of the property is by no means perfect for building. In order to still avoid large amounts of concrete, point foundations were implemented after levelling the ground. Formwork and reinforcement are prepared at the “Makerspace” and put together on site. The transport concrete itself needs to be brought in by means of wheelbarrows, as the truck is too big for the entrance path.
4.2 Floor
After the drying process of the concrete foundations, we implement the sub-construction of the floor was mounted on top. It is made of metal frames that have been treated with a protective coat. The assembly is carried out like a puzzle: The customized and pre-drilled frames are brought to the site and connected right in their final positions. In just a few hours the floor is not only placed but bolted to the foundation.
4.3 Primary Structure
Just like the metal frames of the floor, the primary structure is prefabricated at the "Makerspace". Equally recycled timber slats are cut to length, laminated and treated with linseed oil, making them resistant to rain. The resulting columns and beams were subsequently brought to site and erected in about half a day.
4.4 Roof
Side by side with the preparation of the elements for the primary structure, the beams, rafters, and purlins for the roof were prefabricated. Team effort and dedication allow us to celebrate the topping-out ceremony just three days after the beginning of the actual construction process on site.
4.5 Wall Elements
Just like the rest of the modules, the wall elements were pre-assembled at the "Makerspace". The metal-sheeted packaging material is cut to the envisaged size. Wooden supporting and pre-drilled holes are added. This enables the team on site to connect the walls as soon as they are placed in their final position. At the same time, the roof sheeting is the roof sheeting is purchased and transported to the construction site, being placed as the final building layer.
4.6 Façade
The Southern walls contain large openings for the folding doors. This façade, facing the private zone of the property, is not covered by metal sheeting. Instead, a wooden façade was designed, using differently sized timber sections. This creates a beautiful contrast to the corrugated sheets of the outer “shell” of the building, facing the neighbouring plots.
Simultaneously, doors, windows and hatches are installed, the toilet facility is finalised and a new garden is laid out.
5. Conclusion
In total, the preparation and pre-fabrication have taken roughly two weeks. The actual set up on the property has been carried out in just five days. The keys to his new workshop have been handed over to Khusta on Friday, the 21st of February.
By now (September 2020), Khusta is making intensive use of his new facility. Furthermore, he has added his own touch to the building and extended the garden.
Information
Year: 2020
Courses:
From Wismar University
Architecture
Civil Engineering
Communication Design and Media
From Nelson Mandela University
Development Studies
Electrical Engineering
Human Settlements
Supervisors:
Prof. Silke Flaßnöcker
Kevin Kimwelle
Wolfgang Dörk
Participants:
Carsten Arndt, Mara Biebow, Kelsey Bruce, Lelethu Buso, Sibusiso Dyantyi, Alena Engel, Morten Fuchs, Maximilian Gedamke, Lena Güntsche, Clemens Jopp, Victoria Sophie Langer, Jann Lübbers, Jana Meier, Sophie Meßmer, Sinethemba Mncono, Pia Mohring, Milena Louisa Müller, Frauke Nessler, Moritz Niebler, Likhona Nqunga, Enne Püschel, Dumisani Qwabe, Uta Scheibe, Hlwati Sigqibo, Lea Strauss, Eva Wachauf